Industrial instrumentation is a critical component for controlling and monitoring industrial processes. These tools are used to measure, control, and display various parameters such as temperature, pressure, flow, level, and more. Selecting the right instrumentation can have a direct impact on the quality, efficiency, and productivity of industrial processes. Here are the key factors to consider when purchasing industrial instrumentation:
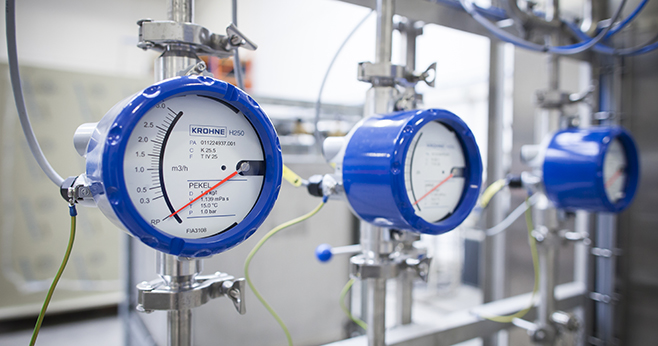
1. Understanding Industrial Requirements
Before anything else, clearly define the specific needs of your industrial process. Key parameters to identify include:
Type of variable to measure (e.g., temperature, pressure, flow)
Required accuracy
Environmental conditions (e.g., temperature, humidity, dust)
Operating range of the instrument (e.g., temperature or pressure range)
2. Accuracy and Precision
One of the most critical criteria when selecting instrumentation is its accuracy and precision. The instrument must provide reliable and precise measurements. Look for equipment with certified calibration certificates to ensure accurate performance.
3. Durability and Resistance
Industrial instruments often operate in harsh environments and challenging conditions. They should be constructed from materials that withstand environmental factors such as high temperatures, humidity, vibrations, corrosive substances, and dust. Instruments with protection ratings such as IP (Ingress Protection) or NEMA standards are excellent choices.
4. Compatibility with Existing Systems
Ensure that the selected instrumentation is compatible with your factory’s existing control system or industrial network. Key aspects to consider include:
Output signal type (analog or digital)
Communication protocols (e.g., Modbus, Profibus, or HART)
Integration with existing monitoring and control systems
5. Response Speed
In processes where rapid changes occur, the response speed of the instrumentation is crucial. The instrument must quickly detect changes and report them to the control system in the shortest possible time.
6. Calibration and Maintenance Capabilities
The instrumentation should allow for periodic calibration to maintain measurement accuracy over time. Ease of maintenance and repair is also essential. Ensure that spare parts are readily available, and the manufacturer provides adequate support services.
7. Compliance with Standards
Instrumentation must comply with national and international industrial standards. Certifications such as ISO, CE, or ATEX indicate the quality and safety of the instrument. This is particularly important for sensitive environments such as chemical or oil and gas industries.
8. Price and Budget
While the price of instrumentation plays a vital role in decision-making, it should not be the sole determining factor. Cheaper instruments may lead to higher long-term costs due to maintenance or frequent failures. Investing in quality and reliability upfront is often more cost-effective.
9. Manufacturer’s Experience and Reputation
Manufacturers with a long history and proven success in the industry usually offer more reliable products. Check customer reviews and testimonials to gauge the reputation and reliability of the brand.
10. Technical Support and After-Sales Services
Ensure that the manufacturer or supplier provides adequate support services, including:
Pre-purchase technical consultation
Training on proper usage
Repair and maintenance services after purchase
Conclusion
Buying industrial instrumentation is a process that requires careful evaluation and analysis of conditions. By considering specific industrial needs, technical specifications, standards, and support services, you can choose an option that enhances the performance, accuracy, and efficiency of your processes. Remember that selecting the right instrumentation not only saves costs but also ensures the quality of the final product.