- Pressure Gauge
- Pressure Transmitter and switch
- Pressure Measurement Accessories
- Temperature Gauge
- Temperature Transmitter and switch
- Level Measurement
- Flow meter
- Valves
- Safety Valves
These pressure gauges operate based on the change in the shape of the steel tubes from the fluid pressure.
Diaphragm plates with resistant materials are used in these gauges as the measuring element. The pressure applied to one side of the diaphragm causes the shape change which this change in shape, leads to the rotary motion of the gauge pointer with a specific mechanism. Diaphragm prevents the direct contact of high temperature or corrosive fluid process with the internal parts of the gauge.
These gauges can also be considered as a kind of diaphragm gauges. Two diaphragms are used in these gauges which the outer edges are welded together. Capsule gauges are used to measure low pressure because these gauges have very high accuracy comparing to other above mentioned gauges.
The process pressure transmitters have been designed for the process industry and using three methods of pressure measuring for gases, steam and fluids. The defined three methods are: absolute pressure, gage pressure and differential pressure.
By deformation of a metal membrane, the electrical resistance changes at the Piezoresistive sensors. This allows for determination of pressure values. Piezoresistive pressure sensors are available as gage, absolute, sealed gage and differential pressure references mounted in either metal or plastic housings.
This sensor measures the difference between two pressures, one connected to each side of the sensor. Differential pressure transmitter also offers continuous level measurement in liquids as well as volume or mass flow measurement.
Different process connections such as threads and flanges with an internal or flush welded diaphragm are available for pressure transmitters.
The output signal is a load-independent direct current from 4 to 20 mA or a PROFIBUS PA or FOUNDATION signal, which is proportional to the input pressure.
Absolute pressure sensor measures the pressure relative to perfect vacuum. Gage pressure sensor measures the pressure relative to atmospheric pressure.
A capacitance pressure sensor has a capacitor that is formed by a static electrode and an opposing movable silicon electrode, and it converts changes in static capacitance that occur when the movable electrode is distorted due to an external force (pressure) into an electrical signal.
Accessories which can be used with gauges if needed:
This accessory is used to isolate the pressure gauges against adhesive or high corrosive fluids.
This accessory is used to block the fluid flow towards the gauge in order to protect the gauge from the pressure which is higher than the gauge over pressure limit.
This accessory is used to control the effect of fluid fluctuations.
This accessory is used to protect the pressure gauge against the high temperature condensable gas or vapour.
Pressure gauges need a valve in order to be connected to the process line, and if the gauge needed any maintenance or change, this manifold helps to only bring the specific gauge out of the line and it prevents the whole process line to be stopped.
In most industrial environment, temperature is one of the quantities which should be measured and controlled. Temperature can be a criterion of reaction progress in a reactor or a criterion of the percentage of components in distillation towers. Temperature increase may lead the Catalysts to be inactive. On the other hand, increase or decrease of the temperature more than the usual limit, may cause the failure in chemical reactions. Therefore, it is vital to have some accessory which can measure and transmit the temperature to the control system.
Temperature gauges, are analog displays which display the temperature of a specific point. The temperature gauges are divided into two categories based on their operation:
The operation of a bimetal temperature gauge is based on the increase or decrease in the length of a metal considering the change in temperature. the advantages of this kind of this temperature gauge is low price, low maintenance need and high and long lasting operation. This temperature gauge can be used in the range of -70 ~ +600 o
The change in the temperature of thermal sensor leads to the change of gas pressure and then the temperature will be displayed. The filled gas should be an inert gas like Nitrogen or Helium. The most important application of gas-actuated thermometers is for the situations which the distance of temperature measuring location with analog display is more than one meter. These temperature gauges can be used in a more wide range than the previous one (-200 ~ +700 oC).
A temperature transmitter combines a temperature sensor (RTD or Thermocouple) and a transmitter that amplifies and transmits the produced analogue or digital output to control device (e.g. PLC, DCS, PC, loop controller, data logger, etc.). Temperature transmitters can support the common industry protocols such as HART, Foundation Fieldbus, Modbus and Profibus.
RTDs – or Resistance Temperature Detectors – are temperature sensors that contain a resistor that changes resistance value as its temperature changes. They have been used for many years to measure temperature in industrial processes. The RTD wire is a pure material, typically platinum, nickel, or copper.
A thermocouple is a simple, robust and cost-effective temperature sensor used in a wide range of temperature measurement processes. It consists of two dissimilar metal wires, joined at one end. This junction is where the temperature is measured. When the junction experiences a change in temperature, a voltage is created; the voltage can then be interpreted.
Thermocouples are available in different combinations of metals. Type J, K, T, & E are Nickel-alloy thermocouples, the most common types of thermocouples. Type R, S, and B thermocouples are Platinum/rhodium-alloy thermocouples, which are used in high temperature applications (up to 1800 °C).
In industrial processes the protection of the thermometers through thermowells and the process connection is important.
Temperature switches measure temperature and activate digital output when measurements exceed the trip point setting. Adjustable temperature switches are perfect for applications which require an economical solution to temperature control.
Level meters are usually used for process control, inventory, custody transfer, the protection and safety, and flow measurement which are installed on top and side of vessels and tanks. Based on applications and the type of process fluids level instruments can be selected and sized. Now with available technology, measurement with high accuracy as well as tenth of millimeter is possible. Based on measurement and transmitting data to operators, there are three types of level instruments: gauges, switches and transmitters.
Level gauges are applicable for operator to use in the field and include of the following types:
– Magnetic
– Transparent Sight Glass
– Reflex Sight Glass
– Float and Servo tank Gauge
Level switches are used for safety applications and turn on and off the pumps and include the following types:
– Cable Float type
– Vibration type
– Conductive type
– Paddle Type
– Capacitance Type
level transmitters are usually smart to send data to control, monitoring and SCADA systems; and support the form of common industry protocols such as HART, Foundation Fieldbus, Modbus and Profibus. The use of this type of instrumentation due to their flexibility in control systems and services that provide for operators is more than two above-mentioned instruments (gauges and switches). It should be noted that the interface measurement is an application of these types of instrument. Transmitter technology are including of the following:
– Ultrasonic Type
– Free Space Radar
– Guided Wave Radar
– Magnetic Level Type
– Displacer Level Type
– Hydrostatic
– Differential Pressure Transmitters
– Radiometric
Flow measuring has great influence on final product quality, safety and process optimization, this is why measuring and controlling flow rate is important in industry. A flow meter is an instrument used to measure linear, nonlinear, mass or volumetric flow rate of a liquid or a gas through a pipe. There are different types of flow measurement such as flow indicators and flow transmitters.
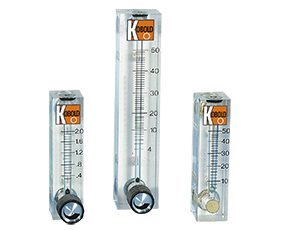
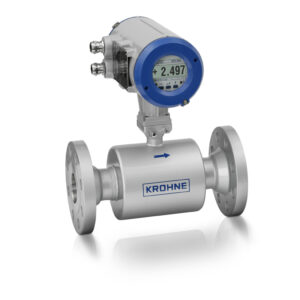
Vortex flow meters operate under the vortex shedding principle, where an oscillating vortexes occur when a fluid flow past a bluff body. In addition to liquid and gas flow measurement, vortex flowmeters are widely used to measure steam flow.
Coriolis mass flowmeters measure the mass flow of liquids, such as water, acids, caustic, chemicals, and gases/vapors by vibrating the tube(s) in which the fluid flows. Because mass flow is measured, the measurement is not affected by fluid density changes. Because of high accuracy they used in metering systems.
A magnetic flow meter is a volumetric flow meter which does not have any moving parts and is ideal for wastewater applications or any dirty liquid which is conductive or water based. The magnetic flow meter requires a conducting fluid that the electrical conductivity is greater than approximately 5μS/cm.
An ultrasonic flow meter is a type of flow meter that measures the velocity of a fluid with ultrasound to calculate volume flow. Ultrasonic flow meters are ideal for applications where low pressure drop, chemical compatibility, and low maintenance are required. It is one of the most common flowmeter in gas metering systems.
As one of the most common technologies for measuring flow in a pipe, Differential pressure flowmeters inferentially measure the flow of liquids, gases and vapor, such as water, cryogenic liquids, chemicals, air, industrial gases, and steam.
Control valves can be called the most important part of the control loop. They act as part of control system to change in process condition. In sizing, selecting the type and material there are challenge between clients and manufacturers, but what we can say the experience is often the decisive factor in the selections. Based on process and control requirement valves can be divided to ON-OFF type and Continuous control type. Except of some cases such as gate valves, generally valves can be used in two operation type (on-off and continuous).
This type of linear control valves are the most common type. Because of their ability to control and flexibility in various applications, they are the first choice in continuous control application.
This type of linear valves has customized application. Generally they used in slurries, high viscosity liquid and low pressure application.
This type of linear valves is used only as ON-OFF operation. They can be used in low pressure and general applications.
This type of rotary valves is used for high pressure and very low leakage applications. In large pipe size, they are better choice to globe valve in continuous control applications. Pressure drop in mentioned valves are less than globe valve.
This type of rotary valves is used in water and waste water industries. They are applicable in high flow rate and low pressure drop conditions.
This type of valve can be seen as a combination of Globe Valve and Ball Valve.
Safety relief pressure valves are used for protection of equipment lines, and tanks along with shutdown systems in refineries, petrochemicals and industries. They act in blocking, fire and thermal expansion cases. In oil and gas industry selection and sizing are based on API standards. Simple operation and self-actuating cause always safety valves to be used in design of process units. Correct selection of valves can reduce the cost impact of events. Constructional material is the major component which affect in price of valves.
They are most common type of safety valve. Their simple operation is the most important of them. They actuated by spring which is set to specific pressure.
Where conventional types are not applicable, the next option is Bellows. Usually this type is used in cases which change of valve back pressure is high or need to protect against corrosion of internal parts of valve.
These types of valves typically are used in cases where both of above cannot be used. Special feature of them is operating at pressures close to normal process pressure. They are the most expensive type of safety valves.
There is another type of safety valves to avoid creating a vacuum in the pressure vessels which are used in large tanks. This type of valves known as vacuum pressure valves.